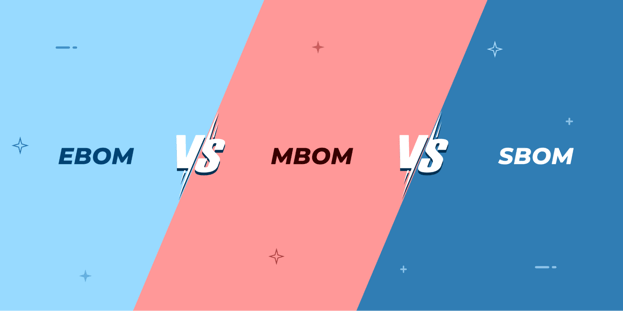
BLOG
BLOG
Managing all aspects of the product development cycle is a crucial element of a profitable company. Most businesses understand that an efficient product lifecycle depends on the proper positioning and management of the Bills of Materials (BOM), be it for product designing and manufacturing or software development.
Getting all the BOMs right is the essential first step toward achieving operational efficiency. However, it's equally important to understand the differences between various types of Bills of Materials. This understanding equips C-suite decision-makers with valuable insights to improve the product manufacturing and service processes.
EBOM (engineering bill of materials) is a document from a design standpoint rather than a manufacturing perspective. Product manufacturing units also consider EBOMs the foundation that provides the directions and components necessary to make any specific product.
An EBOM has the list of items, parts, components, assemblies, and subassemblies in the product in question. Engineers typically create it on various CAD (computer-aided design) and EDA (electronic design automation) tools.
MBOM (manufacturing bill of materials) is a document for manufacturing purposes and reflects how to manufacture the product. It will be organized with the subassemblies reflecting the manufacturing process.
For example, suppose the manufacturing of any product uses ten screws of the same type and size. In that case, the MBOM will list each screw usage in the assembly of the product. On the other hand, the EBOM will list all of those as one and mention ten as the quantity.
An MBOM is the master definition that documents what to make for businesses, while the BOP (bills of process) has complimentary information on how to make the product.
SBOM (software bill of materials) is very contrasting to EBOM and MBOM. It is the primary building block of software security and supply chain risk management. It lists all the ingredients that make up the components of a software.
An SBOM ideally includes the entire inventory of a codebase. This may include open source components and version information, license, and also if there are any vulnerabilities to the listed components.
All of these Bill of Materials: EBOM, MBOM, and SBOM, work together to align all the processes and teams in manufacturing or software development.
While the EBOM and MBOM improve manufacturing effectiveness across all the product-building components and multiple departments and teams, the SBOM is responsible for the software's vulnerability-free development and incident response.
With the proper implementation and management of all the BOMs, teams from supply chain management, purchasing, inventory, operations, engineering, etc., can work together from the same fundamental data.
The integration of all the BOM can:
Modernizing BOM management is imperative, especially since almost every industry is undergoing rapid advancement with its processes and tech stack.
Most modern-day solution suites for BOM management include automation, version controls, and error correction to eliminate manual efforts and inaccuracies. Some key best practices that can ensure effective MBOM, EBOM, and SBOM management include:
It is impossible to remember all the required information in the BOMs manually. However, cloud ERP systems use customizable workflows and wizard-based processes to ensure all required information is included in the BOMs. Businesses can integrate these cloud systems with their existing systems and data sources to ensure the creation of error-free BOMs.
When businesses create bills of materials manually from scratch, there are chances for variations and incompatibilities. However, with the help of modern template-based tools, the BOMs are standard across products and are collaborative and manageable. This means, changing or updating any BOM or related documents instantly is possible without errors.
Testing and checking are standard among all processes in any organization. So, the teams handling the product development lifecycle should integrate the same in the case of bills of materials as well. Automating the BOM creation process using modern-day tools can bring in other features, including built-in audits, intelligent assistance, etc.
Regarding the best practices for BOMs, staying updated with industry regulations and standards around the product is imperative. Businesses should ensure that all BOMs (including SBOMs for IT companies) comply with these requirements to prevent compliance-related issues and maintain customer trust.
Promoting collaboration and communication between engineering, manufacturing, and software development teams is crucial to maintaining effective BOM management. It is vital to encourage cross-functional teams to review and validate BOM data (in the case of manual processes) to ensure consistency and understanding.
Knowing the key differences and best practices with EBOM, MBOM, and SBOM is a crucial element to master for businesses to achieve efficient and accurate product management and development processes.
Seamlessly integrating these three components leads to more efficient manufacturing and development operations, ultimately allowing companies to respond more effectively to market changes and customer needs.
EBOM, MBOM, and SBOM are more than mere acronyms; they can make or break the product manufacturing and service processes. Decision-makers should consider that the three types of BOM create a seamless flow between design, production, and software development.